
Optical and especially components used with X-Rays have some of the finest surface finish requirements achievable. Ship’s propellors start out with fairly high surface finish standards but in actual use they erode pretty quickly. The required surface finishes are very much determined by the function and use of the component. Reducing surface roughness typically reduces friction which can be critical to reducing wear and increasing efficiency of sliding parts. If the casting is too imperfect, the trough of an imperfection may be below the expected machined surface of that future step.Īnother important consideration is friction. For example, we may have a surface finish requirement on a casting that ensures the finish (think of it as the deviations of the surface of the casting from an ideal) is good enough that the allowance made for extra material that will be machined off in a future step is sufficent. There are a variety of considerations, and they may even vary for different stages in the manufacture of a particular part. How do product designers decide what surface finishes to require, and how should CNC machinists think about surface finishes? For example, a surface may be warped or deflected from the ideal. Surface Roughness speaks to fine detail imperfections, but there may also be much coarser irregularities. Surface roughness is usually what machinists refer to when talking about “surface finish.” When talking about all three characteristics, they may use the term “Surface Texture” more properly. Surface roughness is a measure of finely spaced surface irregularities. Surface Finish Lay Patterns… Surface Roughness The Lay is the direction of the predominant surface pattern, and is usually determined by the production method used to process the surface. The relationship of Waviness, Lay, and Roughness… Lay
#Flycut tool for vw how to#
This diagram gives an idea of how to think of the relationship of Waviness, Lay, and Roughness: Another term, analagous to Surface Texture, is Surface Topology. Surface Finish when it is intended to include all three characteristics is often called Surface Texture to avoid confusion, since machinists often refer to Surface Roughness as Surface Finish. Surface Finish is a measure of the overall texture of a surface that is characterized by the lay, surface roughness, and waviness of the surface. Aside from dimensions and tolerances, another important callout is Surface Finish. Engineering prints call out a great many things in their attempt to make sure the part that gets made matches the designer’s intent. 575/.575 HR cam that CR should be fine.Before we get on with Surface Finish Symbols, let’s understand how Surface Finish is defined. I did not want a shim gasket though so I am happy with 9.5 CR. I did not gain a half a point, but the chambers were a little larger than 100cc on average (before cutting) and the added volume of the gasket took away a little as well. The CR I calculated worked out to be about 9.55:1 with a Fel-Pro gasket at. 108.:beers: The additional volume does not hurt my CR that bad. 065 9 degrees after TDC, and now I have about. I also measured the volume of the new valve relief as I cut them to ensure the cuts were equal. I took some pics that I could post if anyone is interested, but they look just like the ones that Vince posted with the exception of the tool. Actually, as crazy as this sounds, it has been one of the easiest things I have done with this motor so far. I basically followed the steps outlined by Vince (thanks again for the pics) and it worked very well. I received the tool from ET Supply and was very satisfied with the quality.
#Flycut tool for vw update#
I thought I would post an update as the motor is mostly assembled now.
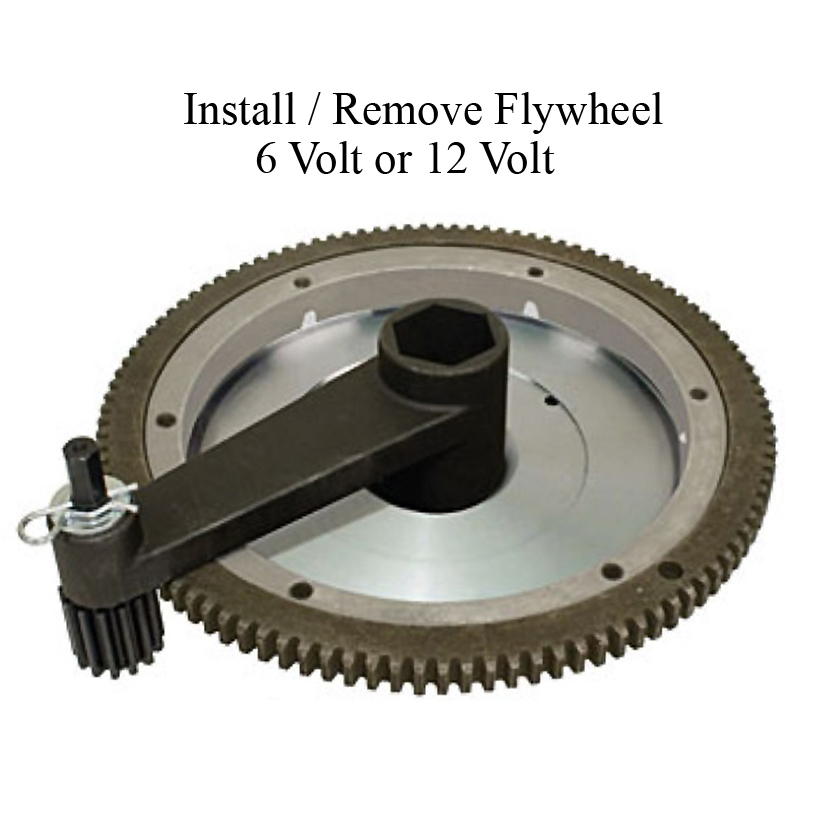
Especially if the exhaust valve has a ton of room.

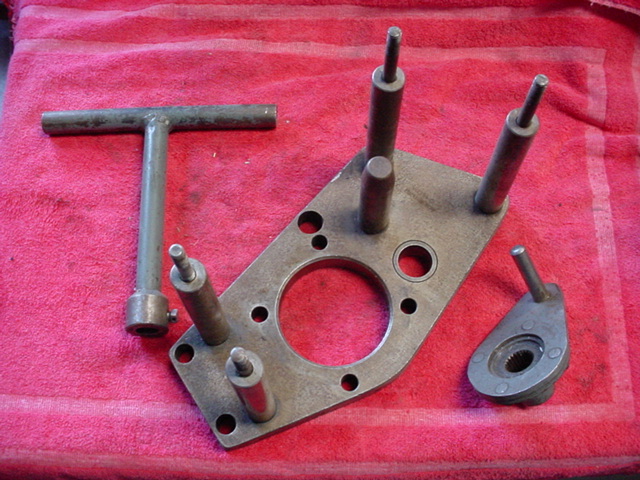
I think the first thing I would do is start from scratch and check the cam degree again. The pistons have to come off the rods, even though I do know one guy that has a fixture for doing them on the rods, but it is a pain in the rear end This way you dont have to cut any more than really needed. If everything is correct and you have to get the pistons flycut, what I like guys to do is get the piston to the point of closest clearance, usually a little before or after tdc, then take the head off and remove the valve and use a transfer punch down through the guide to mark the top of the piston. The cutout might be deep enough, just not big enough in diameter.ĭid you have a head gasket on when you checked it ? that will give you another. It might be just hitting the edge of the valve relief. How much room did the exhaust have ? Also, you need to put some clay on and see exactly where it is too close. I really wonder if you have the cam degreed right, even after your previous post. 625 cams in Mercruiser flat top engines and never had any type of clearance issues.
